Cost Saving Castings and Shafts
If you’re ready to re-source your current machined castings and shafts from China, Century Fasteners has high quality sourcing in Taiwan.
1. Investment Castings – Advantages
The investment casting process offers many benefits including cost savings, design freedom, close tolerances, better finishes, shorter machining time, reproducibility, and assembly savings.
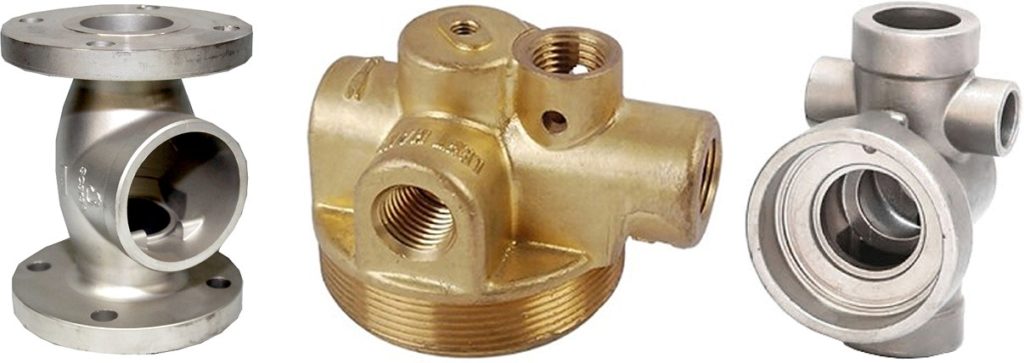
Low Initial Tooling Costs:
Initial tooling costs averaged over the parts produced are often less than other manufacturing tooling costs.
Elimination of Material Waste:
Investment castings are essentially cast to size, thus decreasing the amount of machining required.
Design Flexibility and Capability:
Infinite choice of alloys and design flexibility for internal and external configurations is seen as a plus.
Design Enhancements:
There are no draft requirements in the investment casting process.
Consistency:
The process gives a reliable and consistent product order to order.
Close Tolerances:
Consistently producing close tolerances over other processes, is seen as an advantage.
Surface Finish Improvement:
A surface finish of about 125 RMS is common for an investment casting.
If you need a single piece component to reduce assembly and reassembly time, if you want to eliminate the cost of fabrication and reduce the use of welding, or if you wish to use a casting to reduce machining time, an investment casting would be a wise decision affecting your bottom line profits.
2. Aluminum Castings – Advantages
Aluminum alloys are used in die casting more extensively than alloys of any other base metal. Die cast items made of aluminum are lightweight and have high operating temperature tolerances when compared to other items made with standard die casting alloys. Aluminum alloys have outstanding strength and rigidity properties, and good corrosion resistance and heat dissipation. Aluminum die castings are produced for an array of everyday products including kitchen implements, streetlamp housings, medical equipment, small engine housings, and automotive, marine, and aircraft hardware.
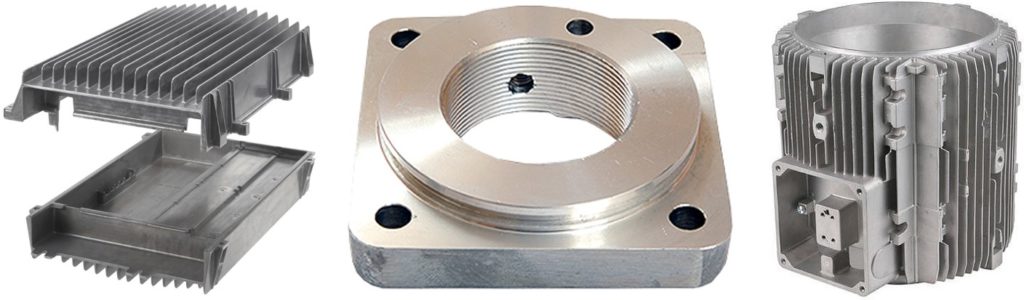
Weight:
Aluminum is light and its density is only one third that of steel.
Temperature:
Highest operating temperatures.
Weather:
Aluminum is resistant to weather, common atmospheric gases, and a wide range of liquids.
Reflectivity:
Aluminum has a high reflectivity, therefore, finds more decorative uses.
Strength:
Aluminum alloys can equal or even exceed the strength of normal construction steel.
Elasticity:
Aluminum has high elasticity, which is an advantage in structures under shock loads.
Toughness:
Aluminum keeps its toughness down to very low temperatures, without becoming brittle like carbon steels.
Conductivity:
Aluminum conducts electricity and heat nearly as well as copper.
Shielding:
Excellent EMI shielding properties.
3. Sand Castings – Advantages
Sand casting’s main advantages as a casting process include relatively inexpensive production costs, the ability to fabricate large components, a capacity for casting both ferrous and non-ferrous materials and a low cost for post-casting tooling.
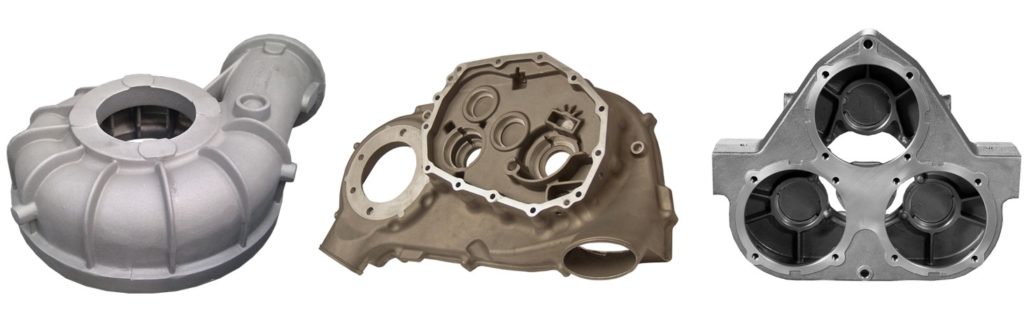
Nearly Any Alloy:
Sand castings can be readily produced in nearly any ferrous or non-ferrous alloy. Some other casting processes will melt and pour super-alloys in vacuum, but that is not typically done as a sand casting. Some materials cannot be “worked”, and must be produced as a casting.
Low Tooling Cost:
The relatively low cost of tooling makes sand casting a process of choice for lower volume needs. Patterns do wear so the material selected for the pattern (typically wood, plastic, or metal) will depend on the expected usage quantity of the part being produced. Though not necessarily cheaper in the short run, the use of machined (or “patternless”) molds may be a cost effective option for components with expected lower usage over a longer period of time.
Versatile – Size, Weight, and Shape:
Sand castings can be produced in weights from ounces to 200+ tons. Through the use of cores, internal structures can be cast in place. Shaped parts rely mainly on the imagination of the designer. Most sand castings, however, will need at least some machined surfaces, either because of innate tolerance limits of the process, or the need to mate with other components.
Any Quantity:
Because the tooling cost can be minimal, sand casting may be appropriate for a single piece run. Alternatively, there are automotive components that are produced using this process, so it may also be used in high volume applications. Other elements of design and tolerance are often more important than quantity when selecting this as the preferred casting process.
Timing:
The casting process itself may be quicker than some others, like investment casting, but it is important to consider the post-casting processes like machining that may be required when computing total lead times.
4. Shafts and Gears
Century Fasteners can work with our Taiwan source to produce high quality Shafts and Gears to meet your requirements. We can supply Shafts and Gears for various industries including Medical, Industrial, Commercial, Automotive and several others.
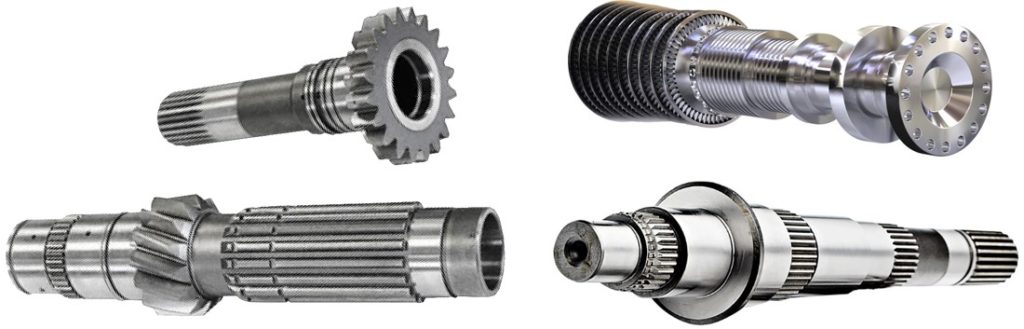
5. We utilize 5-Axis Machining
CNC (Computer Numerical Control) machining refers to the process of removing material with high-speed precision machines that make use of a wide range of cutting tools. 5-axis machining refers to a machines ability to move a tool or a part in five different axes simultaneously. Basic machining operates on three primary axes, X,Y and Z; however, a 5-axis CNC machining tool can rotate two additional axes, A and B, which give the cutting tool a multi-directional approach.
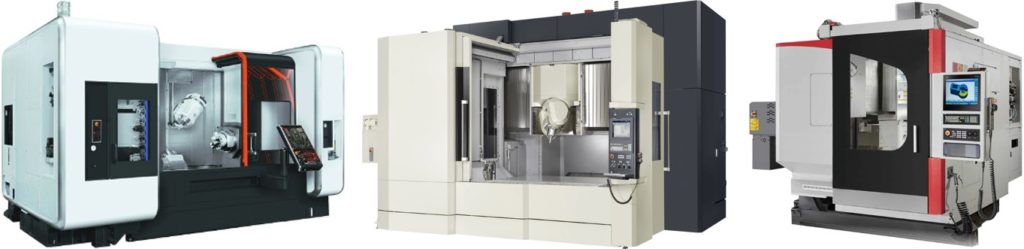
5-Axis Machining vs. 3+2 Axis Machining
5-axis machining offers three linear axes and two rotational axes that work simultaneously to achieve complex surface machining. The 3+2-axis machining offers a 3-axis milling process, with two additional axes to rotate the hold tool in a fixed position as opposed to manipulating it repetitively during the machining process. A 5-axis machine helps you work on tighter tolerances to achieve complex geometries while a 3+2 system allows you to hold your less complex parts in positions that allow better access to the features.
Benefits of 5-axis Machining
5-axis machining helps in the cost effective manufacturing of sophisticated design. The advantages of switching to 5-axis machining include:
Minimized Setup
A 5-axis machine allows you to work on every surface, apart from the clamping area and the bottom. When working on contoured parts or parts that require machining on several faces, you need several setups of the 3-axis machine to achieve the complex geometry through manual rotating; 5-axis technology completes the job in a single set up, reducing the number of setups and helping you save time.
Complex Designs
The additional movement available with 5-axis machining allows you to achieve complex shapes and designs. With the 5-axis machine, you have access to machining angles and arcs that were previously achievable only through multiple setups and a myriad of special fixtures. Ultimately, 5-axis machining eliminates the need to create complex fixtures as you can hold the part once and rotate in a single process to achieve the desired geometry.
Rotational Accuracy
Every time you remove a part from a machine, you lose the precise alignment that allows you to achieve superior quality. Unlike 3-axis machining, 5-axis machining improves accuracy by allowing you to complete a task in a single set up, and create multiple and complex shapes without losing the precision required to maintain quality.
Faster Material Removal
In 5-axis machining, the cutting tool remains tangential to the cutting surface, allowing for low cycle times, which helps save costs as you remove more material each time the tool passes.
Better Surface Finishes
The fourth and fifth axes help you orient and bring the part closer to the cutting tool, allowing you to use a shorter cutting tool, which is less susceptible to vibration at extremely high cutting speeds, helping you achieve a better surface finish. It also saves you time; when using a 3 axis machine, you must make use of very small cuts to achieve a good surface finish, which leads to longer lead times.
For a prompt response, contact:
Director of Business Development
Bob Botticelli 631-339-5353
rbotticelli@centuryfasteners.com