What is Advanced Product Quality Planning (APQP)?
APQP is a structured approach to product and process design. This framework is a standardized set of quality requirements that enable suppliers to design a product that satisfies the customer.
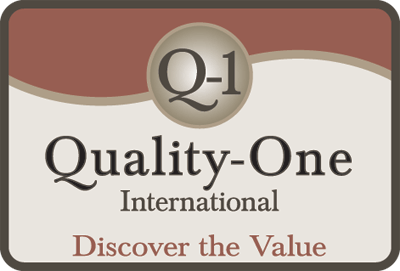
The following information is sourced from the Quality-One International’s website.
Quality-One International offers a plethora of training and certification programs. If you assess the need for training or certification, Quality-One International is an excellent choice! Please visit https://quality-one.com/core-competencies/ for a list of their offerings.
APQP Tools:
There are numerous tools and techniques described within APQP. Below are some common APQP tools:
- Failure Mode and Effects Analysis (FMEA)
- Measurement Systems Analysis (MSA)
- Statistical Process Control (SPC)
- Production Part Approval Process (PPAP)
Why Implement Advanced Product Quality Planning (APQP)?
APQP supports the never-ending pursuit of continuous improvement. The first three sections of APQP focus on planning and prevention and make up 80% of the APQP process. The fourth and fifth sections support the remaining 20% of APQP and focus on validation and evidence. The fifth section specifically allows an organization to communicate learnings and provide feedback to develop standard work and processes.
The APQP Sections are:
(see https://quality-one.com/apqp/ for definitions):
- Section 0: Pre-Planning
- Section 1: Plan and Define
- Section 2: Product Design and Development
- Section 3: Process Design and Development
- Section 4: Product and Process Validation
- Section 5: Feedback Assessment and Corrective Action
When to Apply Advanced Product Quality Planning (APQP):
APQP is used in two scenarios (see https://quality-one.com/apqp/ for definitions):
1. New Product Introduction (NPI)
2. Product or Process Change (Post Release)
APQP Inputs and Outputs by Section:
See https://quality-one.com/apqp/ for more information.
How to Develop a Product Quality Plan (PQP):
The APQP process begins with the creation of a Product Quality Plan (PQP). The PQP may be unique for each individual development. During the planning section, a core group of personnel will review the concept design, process and product assumptions, overall goals of the project and past failures. After collecting this information, the core team selects tools from each section, based on the value they may bring when failure prevention is discussed. The PQP is linked to the project timing plan to aid in program / project management efficiency. The tools and techniques are selected based on what risk may be present, created by the intentional and incidental change. Discovering unknown risk is desirable. Each risk is quantified and mitigation actions are developed and implemented increasing the probability of project success.
Example of a Product Quality Plan:
See https://quality-one.com/apqp/.
How is APQP related to PPAP?
Product Part Approval Process (PPAP) highlights the proof or evidence collected through APQP. Validated results from the first trial run supports the assertion that quality of delivery is expected. The trial run must represent the production environment, with correct tools, machines, processes, personnel and conditions that may affect part quality.
PPAP and APQP cannot be separated, as PPAP documents are the result of APQP. PPAP provides evidence that APQP has been successfully performed. Poor performance in a PPAP or a rejected sample can be attributed to poor APQP. Deliverables in PPAP are extensions of APQP Planning. The PPAP elements can be found at: https://quality-one.com/apqp/.
Additional Guidance:
CFC does not mandate the use of Quality-One International or any other consultant. Quality-One International is a highly competent source of information, and their content is utilized by CFC due to their experience and expertise. CFC’s suppliers are encouraged to consider their capabilities and assess their needs when considering 3rd party help to meet the requirements of contracts they are anticipating to accept or have accepted.
Another useful tool for guidance:
AS9145, Requirements for Advanced Product Quality Planning and Production Part Approval Process.
Century Fasteners Corp.
Director of Quality
Nathan Howell